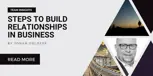
THE PURSUIT OF OPTIMISED MINE PERFORMANCE
By Johan Oelofse
Running a mine efficiently is often the difference between meeting targets or not. Enabling excellence in mineral processing operations requires dedication and ongoing commitment to optimisation.
In the digital era, achieving optimisation requires a multi-pronged approach, relying on a dedicated team of engineers and frontline staff to ensure plant optimisation, while implementing technology solutions that enable remote monitoring and control. With systemic problem-solving capabilities, the right engineers and advisors, and help from modern technology, Minopex Optimisation Services assist customers in solving pressing operations issues in mineral processing.
How to Drive Optimisation in Mining: 6 Steps
There are six steps to achieving optimisation:
- Assess
The assessment phase follows a dual approach; practices and processes. The first; assessing business practices and determining how well the business understands good practices, and how many bad practices it is unaware of. Thereafter a full-scale process modelling and assessment. This pinpoint core focus areas in the facility.
- Standardise
Standardisation forms the base of the optimisation pyramid, followed by stabilisation. In mining optimisation, standardised operations are critical, and involve determining the best way to run the operations and ensuring all frontline staff apply those standards. If you don’t have standardisation, stabilisation is extremely difficult.
- Stabilise
One of the biggest challenges in processing facilities is operational fluctuations. Management teams constantly struggle to get into a good rhythm, which would ensure consistent throughput. To achieve stabilisation, standardisation is required. With the right operational performance visibility and control philosophies in place, a stable process can be realised.
- Visualise Performance
A processing plant has many cogs that run to make it function efficiently. Often, mining optimisation efforts focus on only a few components, to the detriment of the others. The important thing about visualisation and modelling is its ability to connect all these together in an end-to-end value stream. It’s no use focusing on and fixing one area of a plant, it’s a continuous flow and a change in one area impacts many others. With the help of standard processes, technology, and powerful visualisations, a birds-eye view of the entire operation can be established. With this level of insight, informed decisions can be made before critical events happen. This will allow the mine to react quicker to specific events.
- Improve
Once standards are in place, and processes are stable, the operations are able to evaluate which processes can be improved. This is the time to push process boundaries, determine whether machines and equipment are truly working at full capacity, and optimise processes for greater throughput and importantly yield.
- Innovate
Innovation is a big term, and many have varying views on what it truly means. Innovation is a process by which a domain, a product, or a service is advanced by applying new processes, introducing new techniques, or establishing successful ideas to create more value. In the mining optimisation sense, innovation is about more than just technology-driven change; it is an opportunity to help operators, managers and decision makers harness the converging technologies to build an integrated operational ecosystem. The real opportunity is to look beyond technology and enable staff to impact their operations in a positive way.
A Holistic Approach to the Optimisation Journey
Optimisation depends on getting best practise standards in place, applying these standards, ensuring stable performance, developing reliable measurements, creating real time visibility, using data to build models, and using these models to determine gaps and opportunities. True optimisation pulls standardisation, stabilisation, improvement, and innovation together for more efficient performance.
For more information about Minopex’s Optimisation Services, please contact Johan Oelofse at johan.oelofse@minopex.com.
– ENDS –