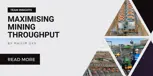
THICKENER OPTIMISATION MAXIMISING MINING THROUGHPUT
Operating equipment efficiently and optimally is vital for maximising long term mining throughput. It is to the detriment of the entire mineral processing operation if even a single units operation is performing sub-optimally. Therefore, continuous optimisation is required to achieve operational excellence.
In the mining sector, especially throughout Africa, water is a scarce yet critical resource. For this reason, mining operations turn to effective water recovery solutions, known as dewatering or thickening processes, that aim to minimise water losses by recycling water to upstream processes. Thickeners are used to enhance the separation process between water and solids, thereby ensuring maximum reuse of water, says Phillip Uys, Metallurgist at Minopex.
This is achieved by separating suspended particles from the liquid through gravity settling. Here, flocculants are used to facilitate the aggregation of particles which promotes settling and aids in separation. Therefore, optimised flocculant and thickener control is a primary focus of the Minopex Operations Team and is essential in achieving the objective of solids concentration and water recovery, he adds.
Evaluating Thickener Performance
It has been identified that slurry density has a major effect on flocculation and can hinder effective settling. According to Uys, the Minopex Operations Team conducted thickener performance tests. These consisted of settling tests which involved:
- In-depth analysis of the thickener feed slurry
- The effect that thickener feed density has on settling rates
The tests were conducted in the metallurgical lab. A sample was obtained from the tailing thickener feed-well to conduct the test and it was found that the sample had a very high density, rating way above design with a high solids concentration. A settling test was conducted on this sample, and it was concluded that there was almost non-existent settling. This means that the particles or solids remain in suspension, and the slurry (mixture between solids and water) stays cloudy. This negatively affects upstream processes where the water is used, explains Uys.
The lab then diluted the same sample down to the design density and solids concentration and conducted the same settling test with the same flocculant. The results showed that the settling rate improved significantly and was aligned with process requirements. Insight was gained that feed slurry without dilution is inadequate for operation.
These tests clearly highlight the effect of dilution on thickener feed slurry, and the important role that it plays in solids settling. The tests demonstrated that effective flocculation can be achieved if the feed material is diluted to design specifications, confirms Uys.It also showed that, at the time, the plant was running its thickener at high feed densities which meant it was not getting the desired settling and that plant throughput rates were adversely affected as there was a build-up of material in the thickener.
Why Invest in Thickener Optimisation and Control?
With a calculated and data driven approach, thickener operation can effectively maximise throughput in mining operations. This is accomplished by:
- Optimal dilution of thickener feed slurry
- Achieving desired thickener settling rates
- Minimising thickener related bottlenecks and plant downtimes
When thickeners are not optimised, there is a negative effect on settling rates which could put the operation at risk. When solids remain in suspension, the thickener overflow water becomes contaminated and negatively affects other upstream processes where this water is used, says Uys.
The Benefits of Optimisation
With a firm understanding of the fundamentals of thickening processes and a complete and comprehensive approach, effective thickener optimisation and control offers the following benefits:
- A clear thickener overflow
- Clean process water that can be used in upstream processes
- No thickener restrictions or bottlenecks
- Operations running at maximum throughput
In summation, an optimised thickener will reduce downtime and unplanned maintenance while increasing production. By overcoming complex technical challenges such as these, the Minopex Operations Team maintains excellent service delivery to the client, concludes Uys.
For more information please contact Phillip Uys at phillip.uys@minopex.com.
– ENDS –